The requirement was to effectively and efficiently error-proof the fixture so that the process could not be completed and the operator could not remove the assembled component without being assured that it had been put together correctly. They needed our Toggle Clamps to provide them feedback that they were closed and apply a Secondary Lock, which would hold the clamp in the activated position until all the operations had been satisfactorily completed. Only at that point, if all operations had been satisfactorily completed, a signal would be given, either a light or a PLC to notify that the assembly had been finished, then the lock would release the clamp, which would allow the operator to undo the clamps and remove the finished component.
What did Sandfield propose as a solution?
The process proposed by Sandfield was that the components should be loaded onto the fixture with proximity sensors that would detect when all of the components were in place.
The next stage would be for the operator to activate the Toggle Clamp, the clamp would then signal to the operator so that they would be assured that it was closed. The Toggle Clamp would only close once all of the components were in place, on receiving the signal the operator could start the assembly. Once the Toggle Clamp was closed the Solenoid Bolt Secondary Lock would be automatically triggered so that the Toggle Clamp could not be opened until the secondary lock was deactivated.
The assembly operation would then be performed including a specific number of tightenings with a torque driver. When they reached the correct number of tightenings and had achieved the required amount of torque the sensors would indicate that the component had been assembled correctly and that the operation was completed. At that point, the Secondary Locking Solenoid Bolt would automatically release and the operator would be able to deactivate the Toggle Clamp and remove the completed component.
If for any reason, they hadn’t completed the required number of tightenings or achieved the required amount of torque, the operator could not physically remove that component from the fixture. This would provide a failsafe method of ensuring that the products had been assembled correctly before they were released.
What were the particular challenges in this project?
The first requirement was supplying a clamp that could signal that it was closed. This is actually a functionality that is an option on a number of Toggle Clamps that Sandfield supply, including the M20 Toggle Clamps that they were already using.
It was the secondary lock, the automated lock, that provided the challenge. At that time we provided the option of an automated secondary lock using a pneumatic cylinder, however, they wanted to power the lock electrically. We had to find an electrical Solenoid Shot Bolt, which we could fit to the clamp that would be robust enough to hold the clamp locked in a closed position. The Solenoid Secondary Lock clearly had to be in proportion to the size of the clamp.
The second challenge was that the fixture had already been manufactured and was in operation so whatever solution we proposed had to be within the constraints of that fixture, to make sure it would fit on the fixture and not get in the way of either the components they are assembling, the fixture or the operator.
Sandfield worked with a solenoid supplier and selected a number of different solenoid switches and produced models. These models were submitted to the customer for selection and approval. Once the customer had selected the model that they felt would best do the job we manufactured prototypes to ensure that the concept was going to work and there were no inherent problems, the big test was to make sure they were strong enough.
One of the unexpected things that we encountered in testing was that whilst the solenoid was actuated and holding the clamp during the process it generated a certain amount of heat. We realised that we would have to design a heat shield that we built around the solenoid to remove the danger of the operator damaging their hands by the heat created by the solenoid.
Because Ford were already using Sandfield Engineering’s M20 Toggle Clamp it made it much simpler for us to take that product and integrate the sensor and the Secondary Locking Solenoid Bolt, which shortened the design and manufacture of the solution considerably.
Are we aware of other Secondary Locking Solenoid Bolt solutions in the market?
Whilst we suspect that similar solutions may have been engineered by Systems Integrators as one-offs previously we can not be sure of that. We are not aware of any of the other clamp manufacturers who have integrated Solenoid Bolt Secondary Locking features into their product rather than build it onto the fixtures. The distinction here is that we were able to produce a solenoid shot switched secondary lock into our Toggle Clamp and have now developed this as a feature or option on a number of the Toggle Clamps in our range.
What other applications are there for a Solenoid Bolt Secondary Locking Toggle Clamp?
The main requirement for a Solenoid Bolt Secondary Locking Toggle Clamp is for error-proofing assembly fixtures. What the Solenoid Bolt Secondary Locking Toggle Clamp is effectively doing is activating a Toggle Clamp. It’s keeping the clamp locked and not releasing it until all of the required number of operations have been completed. Solenoid Bolt Secondary Locking Toggle Clamps can also be used on a curing cycle where a certain amount of time needs to pass before the operator is able to release the clamp.
Toggle Clamps with this functionality are used in a number of operations including welding and glueing, essentially any operation that can be detected by a sensor can be used to automatically trigger the activation or deactivation of the clamp.
What was the outcome of this project?
The only feedback that we have had from the customer (we don’t tend to get much feedback unless there are problems) was that the solution is working, doing exactly what they required of it and had resolved their challenge. You will find a testimonial about his experience with Sandfield Engineering below.
The second outcome is that we now offer Solenoid Bolt Switched Toggle Clamps as an off the shelf product which is available on our range of M20 and M30 Toggle Clamps. We are looking to incorporate this functionality into other clamps that we produce. The main consideration is the size, there is a limit on how small the clamp can be. Providing the clamp is large enough to accommodate the solenoid there is no reason why this technology couldn’t be used on most of the clamps that we supply. If this functionality isn’t currently available on the clamp that you are looking for we could, in most cases, customise it to include a Solenoid Bolt Switch.
If we hadn’t been able to integrate the switch into our clamp the customer would have needed to try and find a way of incorporating the lock into the fixture, and then a way of integrating that with the clamp. The solution we provided was essentially an off the shelf clamp with the solenoid and the sensor all built into one finished product, complete with our clamp guarantee.
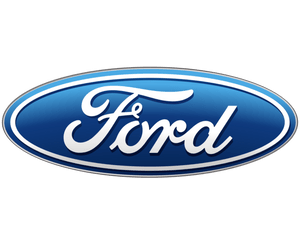